THREAD WHIRLING - WHAT IS IT, AND HOW DOES IT WORK?
WHAT IS THREAD WHIRLING?

Thread Whirling is a form of the Thread Milling process with the exception that the cutters are mounted on the inside of a Cutting Ring or Cutter Holder
rather than the outside of a milling tool.
Recommended Parameters for Thread Whirling
ADVANTAGES OF THREAD WHIRLING
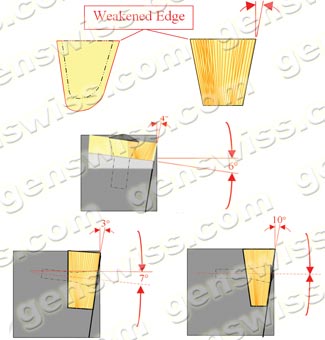
Thread whirling offers several advantages over single point threading:
• Deep Threads - Bone Screws usually have a deep thread formation like Acme forms and other increased pitch threads which can be machined
in less time by whirling.
• Long Length to Diameter Threads - When used on a Swiss Type machine the Thread Whirling Spindle works close to the Guide Bushing
for increased support and rigidity on long length to diameter screws. The process is usually performed in a single pass from stock diameter
which maintains constant material support.
• Faster Setup - By eliminating the need to match rough and finish insert forms the thread whirling process reduces setup and debugging time.
It eliminates special support devices and expensive startup development costs.
• Increased Productivity - A result of cycle reduction and increased up time is greater productivity. Thread Whirling is usually performed in a
single pass from stock diameter. This eliminates multiple passes required for single point threading. By eliminating unnecessary support
devise and multiple thread passes a single cycle can be reduced by minutes.
• Increased Tool Life – Whirling inserts have a stronger cutting edge than single point tools because cutter side clearance is achieved by rotating
the whirling spindle not by relieving material under the cutting edge.
• Cutter Clearance - With a single point threading insert the side strength of the cutting edges are weakened with the additional increased relief. If the helix angle of the thread is 7° then the cutter clearance must be greater 7°.
Lay down inserts may use an anvil under the insert that will accommodate some of the clearance issue. However, 6° is the usually the maximum angle found on standard anvils and the remaining clearance must be made up with relief on the insert itself.
Top notch or side screw inserts would required special holders or would need all of the clearance to be built into the cutter; this would considerably weaken the edge strength. Chip load for whirling is considerably less than single pointing and combined with the increased edge strength it equates to longer tool life and increased production time.
COMPARED PRECISION OF THREADING METHODS
The Thread Whirling process offers many advantages including precision results comparable to other high quality threading methods such as Thread Grinding and Thread Rolling.
GRINDING | ROLLING | WHIRLING | |
---|---|---|---|
Lead accuracy | Very good | Medium; controlled by subsequent heat treatment | Medium; depends on machine accuracy and stress relief |
Diameter control | Very good; direst through steadies and infeed axis | Medium; indirect through bar diameter | Poor; direct, but depends on centering of bar under machining load |
Lead wobble | Very good | Not controlled | Good |
Thread roundness | Verygood | Good | Poor; whirling cannot produce round threads |
Surface finish | Good; depends on wheel used | Depends on polishing process | Good; depends on cutter quality |
R2 - Source of table: August Steinmeyer GmbH und Co. KG, (Bedford, MA) www.steinmeyer.com
Surface Finish –The improvement in surface finish by the thread whirling process is a result of the unique tangential cutter path and the increased rigidity. Burrs are also minimized due to a reduced chip load and longer tool life.
In a comparison to thread milling a 0° thread wall which is commonly found on the trailing side of a bone screws thread, the finish pattern of thread whirling is improved due to the tangential radial entry and exit of the cutter which leaves a uniform pattern.
In the thread whirling process the cutter path enters and exits the cut in a radial arc which is similar to the thread radius direction. As the heel of the insert exits the thread form the resulting finish leaves a cross hatch pattern. This cross hatch pattern would not be seen on any thread wall with a positive wall angle. This is because the cutter only contacts the work piece at the full tangency of the cutting path.
In the thread milling process the cutter path cuts on the way into the cut and up to the full tangent point. As the heel of the cutter makes an exit path the direction of the finish pattern changes as the cutters pull up material as the part rotates into the cutter path; the result is a cross hatch pattern.
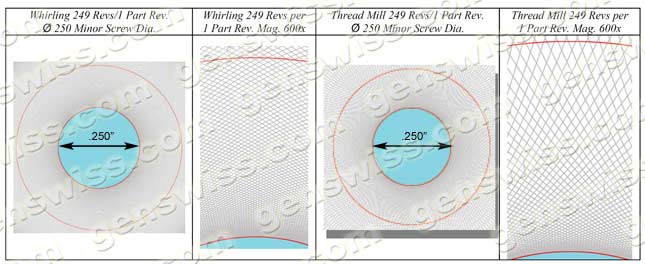
THREAD WHIRL PARAMETERS FOR SUCCESSFUL THREAD GENERATION
THREAD WHIRLING PARAMETERS
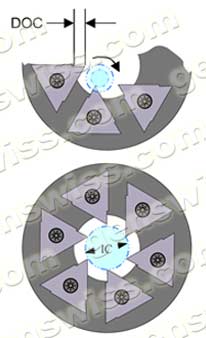
Although Thread Whirling is quite simple there are a few parameters to understand:
1. Can Any Machine Be Used to Whirl? Not every machine can be used for whirling. The machine must be equipped with either a C-axis on the Main Spindle or
Servo Type Main Spindle so can achieve programmed speeds of 10 or 20 RPM.
2. Threading Inserts - To achieve a unique desired thread shape, a special form insert which matches the desired thread form is required.
3. Depth of Cut - The max. DOC is dictated by the insert protrusion relative to the holder. This amount is approximately .100”
4. Maximum Dia. - The max. Diameter is dictated by the inscribed circle between the cutter tips. A clearance between the cutters and the work piece is required if
a rapid retraction is desired.
In rare cases a larger diameter can be achieved up to the IC of the Cutter Ring. This requires the whirling cutters to feed on and then feed off at the same pitch
rate similar to a die. Caution must be taken or the cutters, the cutter ring and the whirling spindle can be severely damaged.
5. Required Passes - With few exceptions, Whirling is generally accomplished in a single pass from stock diameter provided the maximum depth of cut is not exceeded.
6. Helix Angle - During the threading process proper cutter clearance is required to prevent the cutters from chipping out due to increase pressure on the edge. In the Whirling process, the whirling spindle with cutters is set at the thread Helix Angle relative to the part in order to provide the proper clearance on the side of the cutters as the whirling cutters move forward over the part. A cutter set at the wrong helix angle will also produce improper form and burrs.
7. Material That Can Be Whirled - Thread whirling can be accomplished on all metals, including some materials having a pre-hardened condition.
8. RPM - Whirling is more like a milling operation than a turning operation because of the interrupted cut. Therefore, the surface footage used to calculate the RPM is based more around milling.
9. Feed - The feed rate is dictated by the thread lead and is programmed in revolutions of the C-Axis, (main spindle) with a G32 or other programmed TPI G-code. As the speed of the C-Axis RPM increases or decreases the rate of travel of the Z-axis also increases or decreases automatically.
10. Chip load - The chip load is used to calculate the RPM of the C-Axis, (main spindle). This is based upon machining data recommendations for finish milling. Given that milling feeds are based upon heavy milling centers, the chip load is reduced to compensate for the lighter duty tool spindle conditions.
11. High Pressure Coolant - We require the use and of high pressure coolant accurately delivered to the front side of the cutting inserts. This provides the best chip evacuation to reduce the potential risk of fires and for optimizing tool life. If flammable materials are being machined the use of fire detection and fire extinguishing systems must be used
ADDITIONAL PRODUCT INFORMATION AND INFORMATION RESOURCES